High-Quality Horizontal Panel Roll Forming Machine for Efficient Production
By:Admin
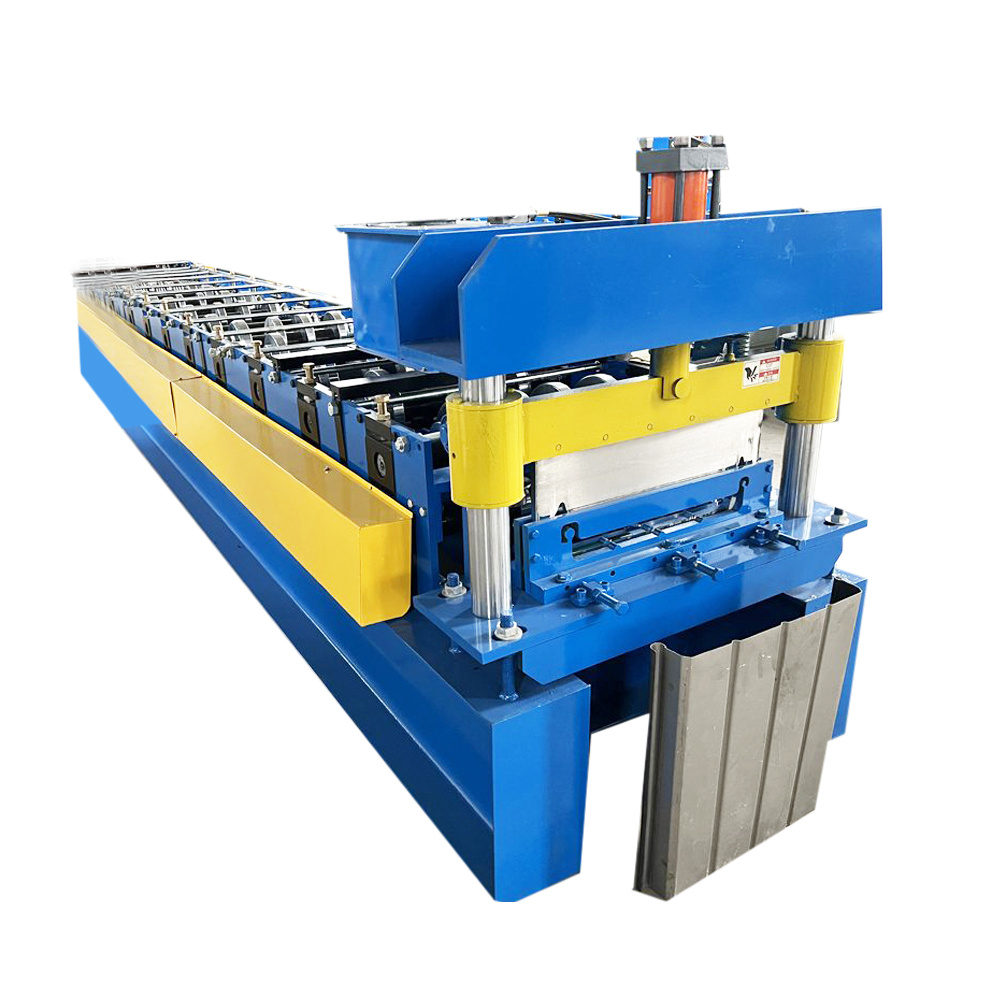
The manufacturing industry has been revolutionized with the introduction of the Horizontal Panel Roll Forming Machine, a state-of-the-art technology that is set to transform the way metal panels are produced. Developed by the leading machinery manufacturing company, [Company Name], this cutting-edge machine has already garnered attention for its innovative design and ability to streamline the production process.
The Horizontal Panel Roll Forming Machine is a game-changer for the manufacturing industry, offering numerous benefits and advantages over traditional methods of metal panel production. It is designed to efficiently produce high-quality metal panels with precision and speed, making it an ideal solution for a wide range of industries, including construction, automotive, and aerospace.
One of the key advantages of the Horizontal Panel Roll Forming Machine is its ability to produce panels with a high level of complexity and variation. This is made possible by the machine's advanced technology and customizable features, which allow for the production of panels in various sizes, shapes, and thicknesses. This level of versatility enables manufacturers to meet the specific needs and requirements of their customers, increasing their competitiveness in the market.
In addition to its versatility, the Horizontal Panel Roll Forming Machine is also known for its efficiency and cost-effectiveness. The machine is designed to operate with minimal waste and energy consumption, helping manufacturers reduce their production costs and environmental impact. Furthermore, its automated operation and smart controls enable higher production speeds and greater output, resulting in a significant increase in overall productivity.
Moreover, the Horizontal Panel Roll Forming Machine is equipped with advanced safety features and ergonomic design, ensuring a safe and comfortable working environment for operators. This not only promotes a higher standard of workplace safety but also improves the overall efficiency and productivity of the manufacturing process.
[Company Name] is a leading manufacturer of machinery and equipment, with a strong reputation for delivering innovative and high-quality solutions to its customers. The company is dedicated to pushing the boundaries of technology and engineering to provide cutting-edge solutions that meet the evolving needs of the manufacturing industry.
With a team of highly skilled engineers and technicians, [Company Name] has been at the forefront of developing advanced machinery that drives efficiency and productivity in manufacturing processes. The Horizontal Panel Roll Forming Machine is the latest addition to the company's impressive portfolio, and it is already making a significant impact in the industry.
The introduction of the Horizontal Panel Roll Forming Machine is a testament to [Company Name]'s commitment to innovation and excellence. By leveraging the latest technology and engineering expertise, the company continues to set new standards in the manufacturing industry, offering solutions that empower businesses to thrive and succeed in a competitive market.
As the manufacturing industry continues to evolve and demand for high-quality, customizable metal panels grows, the Horizontal Panel Roll Forming Machine is expected to play a pivotal role in shaping the future of manufacturing. Its advanced capabilities, efficiency, and cost-effectiveness make it a valuable asset for manufacturers looking to stay ahead in a rapidly changing market.
In conclusion, the Horizontal Panel Roll Forming Machine represents a significant leap forward in the manufacturing industry, offering a range of benefits and advantages that are unmatched by traditional production methods. With its advanced technology, versatility, and efficiency, it is poised to drive innovation and transformation in the way metal panels are produced, setting a new standard for excellence in manufacturing. [Company Name] continues to lead the way in delivering cutting-edge solutions that empower businesses to thrive and succeed in today's dynamic market.
Company News & Blog
Steel Coil Slitter: The Ultimate Guide
Steel Coil Slitter: Enhancing Efficiency and Precision in Metal ProcessingIn the world of metal processing, precision and efficiency are essential components to ensuring high-quality products and optimal production capabilities. One company that has been at the forefront of innovation in this field is {}. With a strong commitment to excellence and a dedication to meeting the evolving needs of the industry, {} has recently introduced its latest innovation – the Steel Coil Slitter.The Steel Coil Slitter is a cutting-edge machine that has been designed to enhance efficiency and precision in the process of slitting steel coils. This state-of-the-art equipment is capable of processing large steel coils into narrower coils of various widths with exceptional accuracy and speed. By utilizing advanced technology and innovative engineering, the Steel Coil Slitter has set a new standard for performance and productivity in the metal processing industry.One of the key features of the Steel Coil Slitter is its ability to accommodate a wide range of coil widths and thicknesses, making it highly versatile and suitable for a variety of applications. This flexibility allows metal processing companies to streamline their operations and achieve greater levels of efficiency in their production processes. Additionally, the Steel Coil Slitter is equipped with precision cutting blades and advanced control systems that ensure consistent and accurate results, minimizing material waste and maximizing the yield of high-quality slit coils.Furthermore, the Steel Coil Slitter is designed with user-friendly interfaces and intuitive controls, facilitating ease of operation and reducing the need for extensive training. This user-centric approach reflects {}'s commitment to delivering innovative solutions that not only optimize performance but also simplify workflow and improve overall productivity.In addition to its impressive performance capabilities, the Steel Coil Slitter is also built with a strong emphasis on durability and reliability. {} has integrated robust construction and high-quality components into the design of the machine, ensuring that it can withstand the demands of heavy-duty industrial applications and deliver consistent results over an extended lifespan. This emphasis on long-term value and reliability underscores {}'s dedication to providing equipment that not only meets current needs but also anticipates future requirements.As a leader in the metal processing equipment industry, {} has a long-standing reputation for delivering cutting-edge solutions that empower metal fabricators, service centers, and other related businesses to achieve their production goals with precision and efficiency. The introduction of the Steel Coil Slitter further solidifies {}'s position as an innovative force in the industry, offering a solution that addresses the complexities and demands of modern metal processing operations.With a focus on continuous improvement and a deep understanding of the evolving needs of the industry, {} has remained dedicated to staying ahead of the curve through research, development, and the integration of the latest technological advancements. The Steel Coil Slitter is a testament to this ongoing commitment, providing metal processing companies with a powerful tool to enhance their capabilities and drive their success in an increasingly competitive market.In conclusion, the Steel Coil Slitter represents a significant advancement in the field of metal processing equipment, offering a compelling combination of precision, efficiency, and versatility. As {} continues to push the boundaries of innovation, it is poised to redefine the standards of excellence in the industry and empower its customers to achieve new levels of productivity and success. With the introduction of the Steel Coil Slitter, {} has once again demonstrated its dedication to delivering state-of-the-art solutions that meet the complex needs of modern metal processing operations.
High-Quality Roll Form Machine for Efficient Production
Roll Form Machine Offers New Solutions for Sheet Metal FabricationSheet metal fabrication is a crucial process in various industries including construction, automotive, and manufacturing. With advancements in technology, the demand for efficient and precise sheet metal fabrication solutions has been increasing. In response to this demand, {company name} has introduced a new roll form machine that is set to revolutionize the sheet metal fabrication process.{Company name} is a leading provider of industrial machinery and equipment, specializing in sheet metal fabrication solutions. With years of experience and a commitment to innovation, the company has built a reputation for delivering high-quality, reliable, and cost-effective machinery for its clients. The introduction of the new roll form machine is a testament to the company's dedication to meeting the evolving needs of the industry.The roll form machine offered by {company name} is designed to streamline the process of shaping and forming sheet metal. It utilizes a series of rollers to gradually bend the metal into the desired shape, allowing for precise and consistent results. The machine is equipped with advanced controls and automation features, enabling operators to easily adjust the settings and parameters to meet the specific requirements of each project.One of the key advantages of the roll form machine is its versatility. It can be used to create a wide range of profiles and shapes, making it suitable for a variety of applications. Whether it's creating corrugated metal panels for roofing, C-channels for structural support, or custom profiles for architectural purposes, the machine offers a flexible and efficient solution for sheet metal fabrication.In addition to its versatility, the roll form machine is also known for its efficiency. With the ability to rapidly and consistently form sheet metal, the machine can significantly reduce production time and labor costs. This makes it an ideal choice for businesses looking to improve their productivity and profitability in sheet metal fabrication.Furthermore, the roll form machine is designed with durability and reliability in mind. It is built to withstand the rigors of heavy-duty use in industrial environments, ensuring long-term performance and minimal downtime. This reliability is backed by {company name}'s commitment to providing comprehensive support and maintenance services for all of its machinery.To complement the roll form machine, {company name} also offers a range of accessories and tooling options to enhance its versatility and adaptability. This includes various sets of rollers, cut-off tools, and end-forming attachments that allow for further customization and specialization in the fabrication process.With the introduction of the new roll form machine, {company name} is poised to further solidify its position as a leader in the sheet metal fabrication industry. By combining cutting-edge technology with a focus on customer satisfaction, the company is empowering businesses to achieve greater efficiency and precision in their fabrication processes."We are thrilled to introduce our new roll form machine to the market," said [Spokesperson], [Position] at {company name}. "We believe that this machine represents a significant advancement in sheet metal fabrication technology and will provide our clients with the tools they need to succeed in their respective industries."As the demand for high-quality sheet metal fabrication solutions continues to grow, {company name} is committed to remaining at the forefront of innovation. With its new roll form machine and a dedication to exceeding customer expectations, the company is well-positioned to meet the evolving needs of the industry and drive the future of sheet metal fabrication.
Efficient and Reliable Sheet Metal Slitter for Industrial Use
48 Sheet Metal Slitter: Revolutionizing Sheet Metal CuttingIn the world of manufacturing and construction, efficiency and precision are key factors in ensuring the success of any project. This is where the 48 Sheet Metal Slitter comes into play. The 48 Sheet Metal Slitter is a cutting-edge piece of equipment that is revolutionizing the way sheet metal is cut and processed.The 48 Sheet Metal Slitter is a powerful and versatile machine that is designed to handle a wide range of sheet metal materials with ease. It is capable of processing sheets up to 48 inches wide and can easily cut through different types of metals including aluminum, stainless steel, and galvanized steel. This makes it an ideal choice for a variety of industries such as HVAC, roofing, and general sheet metal fabrication.One of the key features of the 48 Sheet Metal Slitter is its precision cutting capabilities. It is equipped with high-quality blades that are capable of making clean and accurate cuts, ensuring that the finished product meets the highest standards of quality. This level of precision is essential in industries where exact measurements and cuts are necessary for the assembly of various products and structures.Furthermore, the 48 Sheet Metal Slitter is also known for its efficiency and speed. It is equipped with a powerful motor that allows for quick and efficient processing of sheet metal materials. This not only saves time but also increases productivity, allowing companies to meet tight deadlines and complete projects in a timely manner.In addition to its cutting capabilities, the 48 Sheet Metal Slitter also comes with advanced safety features to ensure the well-being of its operators. It is designed with safety guards and switches to prevent accidents and injuries during operation. This makes it a reliable and safe machine to use in any manufacturing or construction environment.The 48 Sheet Metal Slitter is the brainchild of _, a leading manufacturer of sheet metal processing equipment. With decades of experience in the industry, _ has a solid reputation for producing high-quality and reliable machinery that meets the needs of various industries.The company prides itself on its commitment to innovation and continuous improvement, which is evident in the design and performance of the 48 Sheet Metal Slitter. The machine is the result of extensive research and development, with a focus on meeting the evolving needs of the modern manufacturing and construction sectors.Furthermore, _ provides comprehensive support and service to its customers, ensuring that the 48 Sheet Metal Slitter operates at peak performance at all times. This includes installation, training, and ongoing maintenance, as well as readily available parts and technical assistance when needed.The 48 Sheet Metal Slitter has already made a significant impact in the industry, with many companies reaping the benefits of its cutting-edge technology and unmatched performance. Its ability to streamline the sheet metal cutting process, while maintaining a high level of accuracy and safety, has led to increased efficiency and cost savings for many businesses.As manufacturing and construction continue to evolve, the demand for advanced sheet metal processing equipment such as the 48 Sheet Metal Slitter will only grow. With its impressive capabilities and the backing of _, it is set to become an indispensable tool for any company looking to stay ahead in the competitive industry.In conclusion, the 48 Sheet Metal Slitter is a game-changer in the world of sheet metal processing. Its precision cutting, speed, and safety features, combined with the support of _, make it a valuable asset for any company looking to enhance their manufacturing and construction operations. As the industry continues to advance, the 48 Sheet Metal Slitter will undoubtedly play a crucial role in shaping the future of sheet metal processing.
Learn About the Horizontal Profiled Panel Roll Forming Process
The roll forming process has long been recognized as a highly efficient and cost-effective method for producing continuous lengths of metal profiles with a consistent cross-section. This process involves feeding a metal strip through a series of roll stations, where each station performs a specific bending or forming operation to gradually shape the metal into the desired profile. One of the most commonly used roll forming processes is the Horizontal Profiled Panel Roll Forming Process, which is known for its versatility and ability to produce a wide range of complex profiles.{Company} is a leading manufacturer and supplier of roll forming equipment, known for its innovative and high-quality solutions for the metal forming industry. With over [X] years of experience, {Company} has built a solid reputation for delivering state-of-the-art roll forming machines and providing exceptional customer service to clients worldwide.The Horizontal Profiled Panel Roll Forming Process offered by {Company} is a highly efficient and automated solution for producing a variety of horizontal profiles with precision and consistency. This process involves feeding a metal strip into the roll forming machine, where a series of roll stations work together to gradually bend and form the metal into the desired profile. The flexibility and versatility of this process allow for the production of a wide range of panel profiles, including roofing panels, wall panels, and other structural components used in the construction and manufacturing industries.One of the key benefits of the Horizontal Profiled Panel Roll Forming Process is its ability to produce profiles with a high level of accuracy and repeatability. This ensures that each panel produced is uniform and meets the required specifications, leading to fewer rejects and higher overall production efficiency. Additionally, the automated nature of the process reduces the need for manual labor, leading to savings in labor costs and increased productivity.{Company} has further enhanced the Horizontal Profiled Panel Roll Forming Process with advanced technologies and features to improve its performance and reliability. The integration of computerized controls, precision tooling, and in-line inspection systems ensures that the production process is closely monitored and adjustments can be made in real time to maintain the quality of the profiles being produced. This results in a more streamlined and efficient production process, ultimately leading to higher customer satisfaction and a competitive edge in the market.In addition to its technical capabilities, {Company} also prides itself on its commitment to customer satisfaction and service. The company offers comprehensive support to its clients, including initial consultation and design, installation and training, as well as ongoing maintenance and technical assistance. This personalized approach has allowed {Company} to build long-lasting relationships with its clients and establish itself as a trusted partner in the roll forming industry.The Horizontal Profiled Panel Roll Forming Process offered by {Company} has been widely adopted by manufacturers in various industries, including construction, automotive, and aerospace, due to its versatility, efficiency, and high-quality output. As the demand for custom metal profiles continues to grow, {Company} remains at the forefront of innovation, continuously improving its roll forming solutions to meet the evolving needs of its clients.As the global market for roll formed products continues to expand, {Company} is well-positioned to capitalize on the growing demand for its Horizontal Profiled Panel Roll Forming Process. With its dedication to innovation, quality, and customer satisfaction, {Company} is poised to continue leading the way in the roll forming industry for years to come.
Revolutionary Horizontal Profiled Panel Production Line Boosts Efficiency and Quality
Horizontal Profiled Panel Production Line Presents New Innovations in Manufacturing TechnologyWith a continuous focus on innovation and advanced manufacturing solutions, {Company Name}, a leading global provider of industrial machinery, is proud to introduce its state-of-the-art Horizontal Profiled Panel Production Line. This cutting-edge equipment offers significant advancements in the manufacturing process, promising improved efficiency, durability, and flexibility.The Horizontal Profiled Panel Production Line represents the culmination of years of research, development, and expertise in the field of industrial machinery. Designed to meet the diverse needs of various industries, this production line incorporates advanced technologies to streamline the manufacturing process of profiled panels, optimizing productivity and performance.One of the key features of this new production line is its horizontal orientation, which sets it apart from traditional vertical profiled panel lines. This configuration offers numerous benefits, including enhanced stability and balance during the manufacturing process. By utilizing a horizontal layout, {Company Name} has dramatically minimized vibrations and improved accuracy, leading to a significant reduction in material waste and ensuring consistent product quality.Moreover, the Horizontal Profiled Panel Production Line boasts a range of innovative components that further enhance its efficiency. Equipped with precision cutting tools and advanced laser-guided systems, the line ensures the precise and seamless shaping of panels. This precision allows for seamless integration of various profiled panel types, ranging from corrugated and trapezoidal to architectural and decorative panels. Such flexibility enables manufacturers to cater to the specific requirements of their customers while maintaining superior quality standards.The new production line also incorporates cutting-edge automation technologies to streamline the manufacturing process. Integrated robotic systems enable efficient material handling and reduce the need for human intervention, thereby increasing productivity and minimizing the risk of errors. Additionally, real-time monitoring systems and advanced quality control methods ensure continuous feedback and enable timely adjustments, guaranteeing that each panel meets the highest industry standards.In line with {Company Name}'s commitment to sustainability, the Horizontal Profiled Panel Production Line incorporates energy-saving features, reducing power consumption and minimizing the overall environmental impact. Through efficient energy management systems and smart utilization of resources, the line not only fulfills stringent environmental regulations but also enables manufacturers to significantly reduce operational costs.Furthermore, the Horizontal Profiled Panel Production Line is designed with user-friendliness in mind. An intuitive interface and user-friendly controls allow operators to easily navigate the production process, minimizing downtime and maximizing productivity. To ensure seamless integration into existing manufacturing facilities, {Company Name} offers extensive technical support and customization options according to the specific requirements of each customer.As a global leader in industrial machinery, {Company Name} has an extensive presence and a strong track record of delivering high-quality equipment to industries worldwide. The introduction of the Horizontal Profiled Panel Production Line further solidifies the company's commitment to pushing the boundaries of manufacturing technology and providing innovative solutions to its customers.In conclusion, {Company Name}'s revolutionary Horizontal Profiled Panel Production Line represents a significant leap in manufacturing technology. Through its horizontal orientation, innovative components, automation features, sustainability initiatives, and user-friendly design, this production line offers numerous benefits to manufacturers, including improved efficiency, product quality, and customization options. With this cutting-edge equipment, {Company Name} continues to empower industries across the globe to enhance their production capabilities and achieve unparalleled success.
Get High-Quality Replacement Roof Tiles in Cambridge PE7
In the world of roofing, one of the most important components is the roof tile. Roof tiles come in a range of materials including clay, slate, and concrete. They serve as both a protective barrier for the top of a building and as a decorative element. If you live in or around the Cambridge area and are in need of replacement roof tiles, you have several options to consider.One popular option for replacement roof tiles in Cambridge is to go with a clay tile. Clay tiles are popular in many areas because of their durability, longevity, and aesthetic appeal. They can come in many different styles and colors, which can make them perfect for a range of architectural styles.If you are looking for a more cost-effective option, concrete roof tiles may be the right choice for you. Concrete roof tiles can also come in a range of styles and colors, and are durable and long-lasting. They are also easy to install, which can save you time and money.In addition to the types of roofing materials you choose, you should also consider the quality of the roof tiles themselves. If you go with a cheap or low-quality tile, you may find yourself in need of replacement sooner than you would like. To ensure that you get the best possible quality, make sure to work with a reputable supplier who can provide you with durable and reliable roof tiles.One way to ensure that you get the best quality roof tiles is to work with a supplier that uses the latest roofing technology. One such technology is the Roof Tiles Machine. This machine can create high-quality roof tiles that are both durable and attractive. They are made using state-of-the-art manufacturing techniques that ensure consistency and quality every time.The Roof Tiles Machine uses innovative technology to create custom-made roof tiles that match your specific needs and requirements. This means that you can choose from a range of colors, styles, and finishes to ensure that your roof not only protects your building but looks great too.The process of making roof tiles using the Roof Tiles Machine involves several different stages. First, the raw material is mixed with water and formed into the desired shape. Then, the tiles are dried and fired in a kiln to create a strong and durable final product.If you are in need of replacement roof tiles in the Cambridge area, it is important to find a supplier that uses the latest technology and manufacturing techniques. The Roof Tiles Machine is one such technology that can provide you with the high-quality roof tiles you need to protect your building and enhance its appearance.In conclusion, whether you are looking for replacement roof tiles in Cambridge or elsewhere, there are several factors to consider. The type of material you choose, the quality of the roof tiles themselves, and the manufacturing technology used by your supplier are all important considerations. By working with a reputable supplier who uses the latest technology, such as the Roof Tiles Machine, you can ensure that you get the best possible quality roof tiles for your building.
Ultimate Guide to Horizontal Panel Roll Forming Machine
Horizontal Panel Roll Forming Machine has been a key player in the roll forming industry for over a decade. They have recently introduced their latest innovation, the HPRF-2000, which promises to revolutionize the panel roll forming process. This state-of-the-art machine offers unparalleled precision, speed, and efficiency, making it the perfect solution for businesses looking to streamline their production processes.The HPRF-2000 boasts a number of impressive features that set it apart from other roll forming machines on the market. Its horizontal design allows for seamless operation and easy integration into existing production lines. The machine is also equipped with advanced control systems that ensure the highest level of accuracy and consistency in panel production. This means that businesses can expect superior quality panels with every run of the machine.In addition to its precision, the HPRF-2000 is also incredibly fast and efficient. With its high-speed capabilities, the machine is capable of producing panels at a rate that far exceeds traditional roll forming machines. This increased productivity not only results in higher output, but also significant cost savings for businesses. Furthermore, the HPRF-2000 is designed to minimize material waste, maximizing the use of raw materials and reducing production costs even further.The company behind the HPRF-2000 has a long-standing reputation for delivering top-quality roll forming solutions to a wide range of industries. With a focus on innovation and customer satisfaction, they have become a trusted partner for businesses looking to optimize their production processes. Their team of experts is dedicated to providing tailored solutions that meet the specific needs of each customer, and the introduction of the HPRF-2000 is a testament to their commitment to excellence."We are thrilled to introduce the HPRF-2000 to the market," says a company spokesperson. "This machine represents the next generation of panel roll forming technology, and we are confident that it will greatly benefit our customers. Its precision, speed, and efficiency make it the perfect choice for businesses seeking to improve their production capabilities."The HPRF-2000 has already garnered a great deal of interest from businesses in the automotive, construction, and manufacturing industries, among others. Its ability to produce high-quality panels quickly and cost-effectively has made it an attractive option for companies looking to stay ahead in today's competitive market. Additionally, the machine's versatility allows for the production of a wide variety of panel types, making it suitable for a range of applications.As businesses continue to seek ways to optimize their production processes and improve efficiency, the HPRF-2000 is expected to play a crucial role in meeting their needs. With its cutting-edge technology and track record of performance, it is sure to become a staple in the roll forming industry for years to come.In conclusion, the introduction of the HPRF-2000 by Horizontal Panel Roll Forming Machine represents a significant advancement in the panel roll forming process. With its unparalleled precision, speed, and efficiency, this state-of-the-art machine is poised to revolutionize production for businesses across a wide range of industries. As the company continues to lead the way in roll forming innovation, the HPRF-2000 is set to become a game-changing solution for businesses seeking to optimize their production capabilities.
The Ultimate Guide to C Purline Machines
The {company name} has recently introduced a new state-of-the-art Stacker for the C Purline Machine, adding another impressive piece of equipment to their already extensive portfolio. This new addition is set to revolutionize the production process, offering increased efficiency and productivity for the company and its customers.The C Purline Machine is a crucial component in the production of high-quality purline products, used in construction and infrastructure projects around the world. The addition of the Stacker will streamline the production process, allowing for faster and more accurate stacking of the finished products, ultimately improving the overall output and reducing lead times.The Stacker is designed to work seamlessly with the C Purline Machine, utilizing advanced technology to automate the stacking process. This not only reduces the need for manual labor but also ensures that the finished products are stacked with precision and care, minimizing the risk of damage during transportation and handling. This is a significant advantage for the company, as it will help to reduce waste and improve overall product quality.In addition to the technical benefits of the Stacker, it also offers a number of practical advantages for the company. Its compact design and user-friendly interface make it easy to integrate into the existing production line, requiring minimal setup and training. This means that the company can quickly start reaping the benefits of the new equipment without any significant disruption to their operations.The introduction of the Stacker for the C Purline Machine is a testament to the company's ongoing commitment to innovation and excellence. With a long history of delivering high-quality products and services to its customers, the company has continuously invested in the latest technology to ensure that it remains at the forefront of the industry. This latest addition is a prime example of this dedication, and it is sure to have a positive impact on both the company and its customers.In a statement, the CEO of {company name} expressed his excitement about the new addition, highlighting the potential benefits for the company and its customers. "We are thrilled to introduce the Stacker for the C Purline Machine to our production line," he said. "This new equipment represents a significant step forward for us, allowing us to further improve our efficiency and productivity. We are confident that it will have a positive impact on our operations and enable us to better serve our customers."The Stacker for the C Purline Machine is not only a significant addition to {company name}'s production capabilities but also a clear demonstration of its commitment to providing the highest quality products to its customers. With its advanced technology and practical advantages, this new equipment is set to make a real difference to the company's operations, and it is sure to be warmly welcomed by its customers.In conclusion, the introduction of the Stacker for the C Purline Machine is a major step forward for {company name}. With its potential to improve efficiency, productivity, and product quality, this new addition is set to have a significant impact on the company's operations. As the company continues to invest in the latest technology, it is clear that it remains dedicated to delivering the best possible products and services to its customers, solidifying its position as a leader in the industry.
Latest News: Powerful Corrugation Machine Unveiled for Color Steel Glazed Tile Roof Panels
Roll Forming Machine for Manufacturing Wall Panels
In recent years, there has been an increasing need for high-quality wall panels for use in a variety of applications, from commercial structures to residential homes. To meet this demand, a new system has been developed that has revolutionized the way that wall panels are manufactured. This system, known as the Wall Panel Roll Forming Machine, has quickly become one of the most popular and widely used technologies in the industry.The Wall Panel Roll Forming Machine is essentially a specialized piece of equipment that is designed to take a flat piece of raw material and transform it into a custom-fabricated wall panel. The machine operates on a continuous basis, allowing for a virtually uninterrupted flow of material and seamless production of large quantities of panels. This level of efficiency and consistency is critical for meeting the high demands of modern construction projects.Perhaps the most important aspect of the Wall Panel Roll Forming Machine is its versatility. It is capable of producing wall panels of virtually any size or shape, from standard rectangular panels to more complex designs with intricate curves and details. This opens up possibilities for architects and designers to create truly unique and impressive structures that were previously impossible to construct using traditional methods.One of the key advantages of the Wall Panel Roll Forming Machine is its automation. The technology used in the machine allows for precise control and accuracy in the manufacturing process. This reduces the need for human intervention, which not only increases efficiency but also reduces the chances of errors and defects in the final product. The end result is a high-quality wall panel that meets or exceeds all industry standards and is sure to provide years of reliable service.At the heart of the Wall Panel Roll Forming Machine is the roll forming process. In this process, a sheet of material is passed through a series of rollers that gradually bend and shape it into the desired form. The Wall Panel Roll Forming Machine uses a custom-designed set of rollers that are specifically tailored to the requirements of each individual project. This ensures maximum precision and accuracy in the finished product.Another key advantage of the Wall Panel Roll Forming Machine is its speed of production. Because the machine operates on a continuous basis, it is capable of producing large quantities of high-quality wall panels in a relatively short amount of time. This makes it an ideal solution for construction companies and contractors who need to meet tight deadlines and strict schedules.The Wall Panel Roll Forming Machine is also highly customizable. It can be tailored to fit the specific requirements of each individual project, allowing for a wide range of options in terms of materials, sizes, and shapes. This versatility makes it an ideal choice for architects and designers who need to create unique and innovative structures that require custom-made panels.In conclusion, the Wall Panel Roll Forming Machine is a cutting-edge technology that has changed the way that wall panels are manufactured. Its precision, speed, and versatility have made it an essential tool for construction companies and contractors who need to meet the demands of modern construction projects. With its automation and customization options, it is sure to continue to be a popular choice in the industry for years to come.