- Home
- News
- Application Characteristics of Color Steel Glazed Tile Roll Forming Machine: A Comprehensive Overview
Application Characteristics of Color Steel Glazed Tile Roll Forming Machine: A Comprehensive Overview
By:Admin
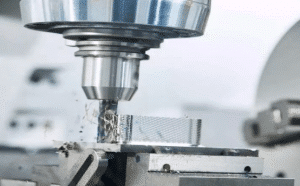
One important component of the color steel glazed tile roll forming machine is the feed introduction platform. This platform is designed to hold the raw materials, typically steel coils, and feed them into the forming process. The platform ensures a smooth and continuous supply of the material, which is critical for the efficiency of the machine.
The forming host is another crucial component of the color steel glazed tile roll forming machine. It is responsible for shaping the steel coil into the desired glazed tile profile. The host uses a series of rollers, each with a specific shape and function, to gradually bend and form the steel coil. This process ensures the accuracy and consistency of each glazed tile produced.
To enhance the strength and durability of the glazed tiles, a die pressing device is incorporated into the machine. This device applies pressure to the tile surface, creating intricate patterns and designs. The die pressing device allows for customization and adds an aesthetic appeal to the glazed tiles.
After the forming process, a forming and shearing device is utilized to cut the continuous profile into individual glazed tiles of the desired length. This device is equipped with precise cutting tools, ensuring clean and accurate cuts without damaging the glazed tile's surface.
Hydraulic stations play a vital role in the operation of color steel glazed tile roll forming machines. They provide the necessary power and pressure for various hydraulic components within the machine. These stations are designed to deliver consistent and reliable hydraulic power, ensuring the smooth functioning of the entire machine.
Lastly, a computer control system is integrated into the color steel glazed tile roll forming machine, allowing for easy operation and monitoring. This system provides operators with real-time information about the production process, including the number of glazed tiles produced, production speed, and any potential issues or errors.
Combined with the extensive experience and expertise of companies specialized in roll forming machines, such as Zhejiang Jinggong Science & Technology Co., Ltd, these color steel glazed tile roll forming machines offer unmatched performance and precision. Companies like Jinggong have been at the forefront of developing advanced technologies and design improvements in the roll forming industry.
As a leader in roll forming machine manufacturing, Zhejiang Jinggong Science & Technology Co., Ltd has a proven track record of delivering high-quality and reliable machines to their customers. With a focus on technological innovation and customer satisfaction, Jinggong strives to meet the diverse needs of the construction industry.
In conclusion, color steel glazed tile roll forming machines demonstrate specific characteristics that make them highly efficient and dependable in the production of glazed tiles. The composition of feed introduction platforms, forming hosts, die pressing devices, forming and shearing devices, hydraulic stations, and computer control systems ensures superior performance and precise tile production. With companies like Zhejiang Jinggong Science & Technology Co., Ltd leading the way, the roll forming machine industry continues to evolve and deliver innovative solutions to the construction industry.
Company News & Blog
Get High-Quality Glazed Tile Roof Panel Roll Forming Machines in Kenya
Glazed Tile Roof Panel Roll Forming Machine is a revolutionary creation in the roofing industry. Its introduction is a significant milestone in fulfilling the roofing needs of millions of people across the globe. This machine is designed to cater to all the demands of both commercial and residential buildings. The Glazed Tile Roof Panel Roll forming Machine is an exclusive production of (need remove brand name), which is a reputed manufacturer of high-quality roll forming machines.The (need remove brand name) has been committed to providing state-of-the-art equipment for the metalworking industry for decades. They are a globally renowned roll forming machine manufacturer, with an extensive network of customers in over 50 countries worldwide. They have a team of experienced professionals who are dedicated to designing, developing, and manufacturing high-quality roll forming machines. Their products are manufactured with precision, meeting the most stringent quality standards, and hence, the company has an excellent reputation in the market.The traditional roofing materials have been replaced by modern ones to provide better energy efficiency, aesthetics, and durability. Glazed Tile roofing panels have become increasingly popular in recent times due to their superior performance characteristics. These panels are made up of galvanized steel sheets, which are coated with several layers of paint to give them a glossy finish. The glazed tile roofing panels are perfect for commercial and residential buildings due to their insulation properties, durability, and lightweight.The Glazed Tile Roof Panel Roll Forming Machine is designed to produce perfect glazed tile roofing panels. The machine uses advanced technology that ensures that the produced panels have high precision and good quality. The roofing panels produced by this machine have an impressive lifespan, with the ability to resist all harsh weather conditions, including extreme heat, wind, and heavy rainfall.The Glazed Tile Roof Panel Roll Forming Machine is a fully automated machine that has been enhanced by modern technology to ensure high efficiency and productivity. The machine is designed with user-friendly features that enable the operator to produce high-quality products with ease. The machine’s automated control system ensures that the rollers automatically adjust their position based on the specifications provided, thus avoiding any manual interventions in the process.Moreover, the Glazed Tile Roof Panel Roll Forming Machine is designed to be reliable, durable, and easy to maintain. The company provides a comprehensive after-sales support service, which includes training and ongoing technical support, to ensure that clients always get the best results from their machines. Also, the machine is built with the latest technology, which ensures that its energy consumption is minimal.In conclusion, the Glazed Tile Roof Panel Roll Forming Machine is an innovative solution for roofing needs. Its introduction is a significant milestone in fulfilling the roofing demands of millions of people worldwide. The machine is designed to cater to both commercial and residential buildings' roofing needs. It is an exclusive production of (need remove brand name), which is a highly reputable and experienced manufacturer of roll forming machines. The Glazed Tile Roof Panel Roll Forming Machine is reliable, durable, and easy to maintain, and customers can count on its excellent quality and performance. The machine is a must-have for any business or individual seeking high-quality roofing solutions.
Glazed Tile Roll Forming Machine - Industrial Steel Rolling Machines for Metal Roofing Sheet Production
Title: ZhongTuoCN Revolutionizes Roofing Industry with Advanced Glazed Tile Roll Forming MachineIntroduction:ZhongTuoCN, a renowned leader in the steel rolling machine industry, has unveiled its latest product, the Color Steel Glazed Roof Tile Roll Forming Machine. This advanced machinery has revolutionized the roofing industry by enabling the efficient production of high-quality metal glazed tiles. With its cutting-edge technology and precision engineering, ZhongTuoCN is empowering manufacturers to meet growing demands for durable and aesthetically pleasing roofing solutions.1. Meeting the Rising Demand for Glazed Roofing Tiles:The demand for glazed roofing tiles has been steadily increasing due to their exceptional durability, weather resistance, and stunning visual appeal. Recognizing this trend, ZhongTuoCN's engineers have developed a state-of-the-art roll forming machine specifically designed to cater to this niche segment. Manufacturers can now produce glazed tiles efficiently, ensuring timely delivery and meeting customer expectations.2. Cutting-Edge Technology Enhances Efficiency:The Color Steel Glazed Roof Tile Roll Forming Machine stands out for its advanced features, guaranteeing optimal efficiency. Equipped with state-of-the-art automation technology, this innovative machine minimizes human intervention, reducing labor costs and increasing productivity. With high-speed forming capabilities, it guarantees a smooth and streamlined production process, allowing manufacturers to meet large-scale orders efficiently.3. Unparalleled Precision and Durability:ZhongTuoCN's Glazed Tile Roll Forming Machine is meticulously engineered to deliver unmatched precision and durability. Its robust frame, constructed from high-quality steel, ensures long-term stability and reliability. The rollers are made from top-grade materials, facilitating seamless tile formation without any deformities. This ensures that every finished tile exhibits consistent dimensions and exceptional surface quality.4. Flexibility in Tile Design and Customization:In addition to its standard features, the Color Steel Glazed Roof Tile Roll Forming Machine provides manufacturers with unparalleled flexibility in tile design and customization. By incorporating adjustable features in the machine, manufacturers can easily tailor the dimensions, profile, and curvature of the glazed tiles to meet various customer requirements. This adaptability sets ZhongTuoCN's machinery apart from its competitors and allows clients to offer unique and personalized roofing solutions.5. Strict Quality Control and After-Sales Support:ZhongTuoCN prioritizes quality control throughout the manufacturing process. Each component of the Glazed Tile Roll Forming Machine undergoes stringent testing to ensure optimal performance and durability. Additionally, ZhongTuoCN provides comprehensive after-sales support, including installation guidance, training programs, and 24/7 technical assistance. This commitment to customer satisfaction has earned the company an excellent reputation in the industry.Conclusion:With the introduction of the Color Steel Glazed Roof Tile Roll Forming Machine, ZhongTuoCN has reaffirmed its position as a pioneer in the steel rolling machine industry. This cutting-edge technology guarantees exceptional efficiency, precision, and customization options for manufacturers in the roofing sector. By empowering clients to meet the rising demand for glazed tiles, ZhongTuoCN is revolutionizing the roofing industry and offering an unparalleled solution for businesses worldwide.
Master the Art of Making Authentic Pasta at Home with a Manual Pasta Machine
Title: Master the Art of Homemade Pasta with a Manual Pasta Machine Introduction (approximately 100 words):Fresh, homemade pasta is a culinary delight that can be easily made in the comfort of your own kitchen. With a few simple ingredients, you can create a variety of pasta dishes that will impress your family and friends. If you're new to the world of pasta making or looking to elevate your skills, investing in a manual pasta machine can make the process much easier and enjoyable. In this blog, we will explore the benefits of using a manual pasta machine and provide an in-depth guide on how to make authentic pasta at home. Body:1. The Advantages of Using a Manual Pasta Machine (approximately 200 words):A manual pasta machine offers numerous advantages when it comes to making homemade pasta. Here are some key benefits:a) Efficiency: A manual pasta machine helps streamline the process of rolling and shaping pasta dough, saving you time and effort compared to manual techniques.b) Consistency: With a pasta machine, you can achieve consistent thickness and shape throughout your pasta, ensuring even cooking and a professional result every time.c) Versatility: Manual pasta machines often come with a variety of attachments, allowing you to create different types of pasta, including spaghetti, fettuccine, and lasagna sheets.d) Authenticity: By using a manual pasta machine, you can replicate the traditional techniques used by Italian nonnas for generations, resulting in truly authentic pasta.2. Getting Started with a Manual Pasta Machine (approximately 200 words):Before diving into the pasta-making process, it's important to familiarize yourself with your manual pasta machine. While models may vary slightly, the general steps and techniques remain the same. Follow these guidelines to get started:a) Preparation: Begin by gathering your ingredients – typically flour, eggs, and salt – and combine them to form a dough. Allow the dough to rest for 30 minutes, as this will make it easier to work with.b) Setting up the Machine: Attach the appropriate cutting attachment to the machine, depending on the type of pasta you want to make. Most manual pasta machines have adjustable thickness settings, so start with the widest setting and gradually work your way down to achieve your desired thickness.c) Rolling the Dough: Divide the dough into manageable portions and flatten each one with your hands. Feed the dough through the machine, starting at the widest setting. Fold the dough in half after each pass and repeat this process until the desired thickness is achieved.d) Shaping the Pasta: Once the pasta sheet reaches the desired thickness, switch to the cutting attachment for your chosen pasta shape. Pass the pasta sheet through the machine, and voila! You have freshly cut pasta ready for cooking.3. Cleaning and Maintenance Tips for Your Manual Pasta Machine (approximately 200 words):To ensure your manual pasta machine remains in optimal condition and longevity, it's essential to follow proper cleaning and maintenance procedures. Here are some useful tips:a) Basic Cleaning: After use, wipe away any excess flour or dough from the machine using a dry cloth or brush. Avoid using water to clean the machine, as this can cause rusting or damage.b) Thorough Cleaning: Periodically, disassemble the machine as per the manufacturer's instructions and clean each component thoroughly. Use warm, soapy water and a soft brush to remove any stubborn residue.c) Drying and Storage: After cleaning, ensure that all parts of the machine are completely dry before reassembling and storing it in a dry place. Avoid exposure to humidity or extreme temperatures, as this can affect its performance.Conclusion (approximately 100 words):Investing in a manual pasta machine can transform your pasta-making experience, allowing you to effortlessly create authentic and delicious homemade pasta. Whether you're a culinary enthusiast or a novice in the kitchen, using a manual pasta machine will streamline the process, offering you consistent results and a variety of pasta types. With the right techniques and maintenance, you'll be able to enjoy countless pasta dishes that will rival those from your favorite Italian restaurant. So, why wait? Start your pasta-making journey today and unlock a world of culinary possibilities!Keywords: manual pasta machine, homemade pasta, authentic pasta, pasta-making, Italian nonnas, manual techniques, pasta dough, cutting attachment, cleaning and maintenance, pasta types.
Premium Steel Sheets: Cut-to-Length, Shear and Slitter Cut Services at Unbeatable Prices!
Title: Enhance Your Project's Efficiency and Quality with Hot Rolled Slitter Steel SheetsIntroductionIn today's fast-paced construction and manufacturing industries, the demand for high-quality steel sheets that can be customized to specific requirements is at an all-time high. Hot rolled steel sheets have become an exceptionally popular choice due to their durability and versatility.This blog aims to shed light on the benefits and applications of hot rolled steel sheets and the key role played by slitter cutting services in meeting the varied needs of different projects. So, let's delve deeper into the world of hot rolled slitter steel sheets!Understanding Hot Rolled Steel SheetsHot rolled steel sheets are produced through a process involving heating steel slabs above their recrystallization temperature, followed by cooling them to room temperature. This technique results in a flexible, strong, and malleable steel product that can be further processed to various specifications. The hot rolling process eliminates impurities, while the controlled cooling ensures uniformity and consistency in the sheet's strength.Applications and Advantages1. Versatility: One of the primary benefits of hot rolled steel sheets lies in their versatility. From automotive manufacturing and construction to machinery fabrication and shipbuilding, these sheets find application across a wide range of industries. Their strength and malleability allow for seamless forming and shaping, making them suitable for diverse projects.2. Durability: Hot rolled steel sheets are known for their exceptional durability. They can withstand heavy loads, extreme temperatures, and harsh environments, ensuring a longer lifespan for your projects. Whether it's a structural application or a component in heavy machinery, hot rolled steel sheets provide the necessary strength and resilience.3. Cost-effectiveness: With their cost-effective production process, hot rolled steel sheets offer excellent value for money. Affordable and readily available, they are a preferred choice for projects that demand a high-volume supply of steel sheets without compromising on quality.The Role of Slitter Cutting ServicesTo maximize the benefits of hot rolled steel sheets, slitter cutting services come into play. Slitter cut refers to the process of cutting wide coils of steel into narrower strips, catering to specific project requirements. This technique ensures precision and accuracy, ensuring that the sheets are tailored to the desired dimensions.Importance of Slitter Cutting1. Customization: Slitter cutting enables customization by accommodating different project needs. Sheets can be cut into a variety of widths, lengths, and thicknesses, ensuring an exact fit for your project requirements. This flexibility eliminates the need for additional processing and minimizes waste, thereby optimizing overall efficiency and cost-effectiveness.2. Simplicity and Time Efficiency: Slitter cutting services streamline the manufacturing process by providing ready-to-use steel strips. This eliminates the need for additional cutting and reduces the time and effort spent in modifying the sheets on-site. Better time management and enhanced simplicity contribute to meeting project deadlines and improving overall work efficiency.3. Precision and Quality: Slitter cutting techniques ensure precise and accurate cuts, resulting in high-quality steel strips. The accurate dimensions obtained through slitter cutting services reduce the risk of errors and ensure a perfect fit for your project's requirements. This level of precision translates into improved structural integrity and better overall performance.ConclusionHot rolled slitter steel sheets offer a range of benefits that meet the demands of various industries. Their versatility, durability, and cost-effectiveness make them an ideal choice for your projects. By employing slitter cutting services, you can further enhance the efficiency and quality of your projects. Customization, time efficiency, and precision are some of the significant advantages that slitter cutting brings to the table.When sourcing steel sheets, consider partnering with a reliable supplier offering hot rolled slitter steel sheets. By doing so, you can rest assured that you will receive quality products that are tailored to your exact requirements. Remember, investing in high-quality materials and services ensures the success and longevity of your projects in the long run.So, why wait? Embrace the versatility and reliability of hot rolled slitter steel sheets for your next construction or manufacturing project, and witness the remarkable difference it can make!
Competitive Intelligence by Key Players in the Automatic Roll Forming Machine Market: Global Market Analysis and Size
Automatic Roll Forming Machine Market: Increasing Industrialization Driving Demand for C/Z Purlin Roll Forming MachinesThe global Automatic Roll Forming Machine market is expected to witness robust growth in the coming years, driven by increasing industrialization across the globe. The Automatic Roll Forming Machine is a highly versatile equipment that is used in industries such as construction, automotive, electronics, and aerospace, among others. It is used for forming metal sheets and strips into different shapes and sizes. Among the various types of Roll Forming Machines, C/Z Purlin Roll Forming Machine is a popular choice for manufacturing structures that require strong supports for roofing, cladding, and walls.C/Z Purlin Roll Forming Machine is a type of Roll Forming Machine that is designed specifically for producing C-shaped and Z-shaped purlins. These purlins are used for making pre-engineered steel buildings, industrial sheds, warehouses, and other structures. The machine works by feeding a strip of metal through a series of rollers that shape the metal into the desired profile. The final product is a strong, lightweight, and durable purlin that can withstand heavy loads and adverse weather conditions.Key Market Players in Automatic Roll Forming Machine MarketThe key market players in the Automatic Roll Forming Machine market include Bradbury Group, Framing Tech, Formtek Group, Gasparini Industries, HILALMAK, Howick, Isolaminas, JET USA, Knauer Engineering, L.B. Bohle Maschinen + Verfahren, M.Torres, Onward Machinery, PEP brainin, Taicang Keboer, TOX Pressotechnik, TRL Krosaki Refractories Limited, Xiamen Zheng Liming Metallurgical Machinery, and Yoder.Market SegmentationThe global Automatic Roll Forming Machine market can be segmented based on product type, application, and region.Based on Product Type, the market can be segmented into:• C/Z Purlin Roll Forming Machine• Corrugated Sheet Roll Forming Machine• Tile Roll Forming Machine• OthersBased on Application, the market can be segmented into:• Construction• Automotive• Electronics• Aerospace• OthersBased on Region, the market can be segmented into:• North America• Europe• Asia-Pacific• Middle East and Africa• South AmericaRegional AnalysisThe Asia-Pacific region is expected to dominate the Automatic Roll Forming Machine market in the forecast period, owing to the increasing demand for industrialization in countries such as China, India, and Japan. The region also has a large base of manufacturers and a significant consumer base for Roll Forming Machines. The North American and European markets are also expected to witness steady growth due to the increasing demand for lightweight and durable materials in the construction and automotive industries.ConclusionThe Automatic Roll Forming Machine market is expected to witness robust growth in the coming years, owing to the increasing demand for lightweight and durable materials in the construction, automotive, electronics, and aerospace industries. C/Z Purlin Roll Forming Machines are expected to witness significant demand, owing to the increasing demand for pre-engineered steel buildings, industrial sheds, and warehouses. The Asia-Pacific region is expected to dominate the market, owing to the increasing demand for industrialization in the region. The key market players in the market are Bradbury Group, Framing Tech, Formtek Group, Gasparini Industries, HILALMAK, among others.
Get Comprehensive Roll Forming Solutions from a Cold Roll Forming Manufacturer in China
Title: Unleashing the Potential of Roll Forming Machines in Metal Roofing ApplicationsIntroduction:Metal roofing has long been a popular choice for both residential and commercial buildings due to its durability, cost-effectiveness, and aesthetics. Behind the scenes, the production of metal roofing materials has been revolutionized by advanced machinery known as roll forming machines. In this blog, we will explore the endless possibilities of roll forming machines in the metal roofing industry, highlighting their crucial role in shaping the sector's future. While focusing on the broader concepts, we will delve into the specific applications and benefits of these machines, allowing us to understand why they are considered the go-to solution for metal roofing manufacturers worldwide.Understanding Roll Forming Machines:Roll forming machines are powerful mechanical equipment designed to transform a continuous metal strip into finished products with predetermined shapes and sizes. They utilize a series of rollers and dies to progressively bend, fold, and shape the metal strip while anticipating any potential deformations, hence ensuring precise measurements and consistent quality output. This process is known as roll forming, and it plays a vital role in the production of metal roofing panels, profiles, and accessories.Applications of Roll Forming Machines in Metal Roofing:1. Metal Roofing Panels:Roll forming machines are the backbone of metal roofing panel production. With their ability to process various metals such as steel, aluminum, and copper, these machines can shape panels with different profiles, including corrugated, standing seam, and concealed fastener systems. The versatility of roll forming machines enables manufacturers to cater to diverse customer requirements efficiently.2. Panel Accessories:Besides creating roofing panels, roll forming machines are indispensable in manufacturing various metal roofing accessories. These include ridge caps, eave trims, flashing, drip edges, and gutter systems. The machines' precision and speed enable companies to produce these accessories with ease, meeting the specific design and functionality demands of each project.3. Other Metal Roofing Components:Roll forming machines can also fabricate a wide range of other key components used in metal roofing systems. These may include purlins, hat channels, framing members, and structural profiles. The ability to produce these components in-house not only offers cost savings but also ensures the compatibility and quality of the final roofing system.Benefits of Roll Forming Machines in Metal Roofing:1. High Efficiency and Cost-saving:Roll forming machines operate at impressive speeds, allowing manufacturers to produce large quantities of metal roofing materials in significantly less time compared to traditional methods. This efficiency translates into reduced labor costs, increased productivity, and higher profit margins.2. Customization and Flexibility:With the ability to adapt to various shapes, sizes, and profiles, roll forming machines open up a realm of customization possibilities. Manufacturers can easily switch between different designs, patterns, and materials, ensuring each client's unique vision is brought to life flawlessly. This flexibility is a significant selling point for metal roofing businesses looking to provide tailored solutions to their customers.3. Consistent Quality and Precision:Roll forming machines possess advanced automation features, ensuring highly accurate and consistent product output throughout the entire manufacturing process. With minimal human intervention, the risk of errors, deformations, or irregularities is significantly reduced. This results in superior quality metal roofing materials that meet or exceed industry standards.4. Reduced Material Waste:Roll forming machines are designed to maximize material utilization, minimizing waste and increasing cost-effectiveness. By implementing computer-controlled cutting mechanisms, these machines optimize the use of metal coils, significantly reducing scrap and enhancing the overall sustainability of the manufacturing process.Conclusion:Roll forming machines have revolutionized the metal roofing industry, enabling manufacturers to streamline their production processes and deliver high-quality, customized roofing materials efficiently. The ability to produce various roofing panels, accessories, and components with utmost precision, flexibility, and cost-effectiveness has made roll forming machines an indispensable asset in the sector. As the metal roofing market continues to grow, businesses that adopt these advanced machines will undoubtedly have a competitive edge, satisfying the ever-evolving demands of customers worldwide. Keywords: Roofing metal forming machine, roll forming, metal roofing panels, metal roofing accessories, metal roofing components, efficiency, customization, quality, material waste.
Interchangeable Purlin Roll Forming Machine for Steel Processing
Title: Streamlining Steel Processing with CZ Interchange Purlin Roll Forming MachinesIntroduction:In the realm of steel processing, efficiency and precision are key characteristics that define success. CZ interchange purlin roll forming machines have emerged as a game-changer in the industry, offering exceptional quality and versatility. This article delves into the advantages and applications of these cutting-edge machines, shedding light on their ability to shape and transform various materials with ease.Advantages of CZ Interchange Purlin Roll Forming Machines:1. Wide range of material compatibility:CZ interchange purlin roll forming machines are designed to process material thicknesses ranging from 1.5mm to 3.0mm. This versatility allows manufacturers to work with diverse materials, expanding their product offerings and catering to the specific requirements of their clients.2. Flexibility in shape and size:These machines are capable of producing both C and Z-shaped purlins, allowing manufacturers to meet the demands of different construction projects. The C and Z sizes can vary from 80mm to 300mm, providing an extensive range of options for construction applications.3. Easy transition between C and Z shapes:With the ability to easily switch from one shape to another, CZ interchange purlin roll forming machines offer unparalleled flexibility. This feature saves valuable time and effort, eliminating the need for additional equipment or complex adjustments. Manufacturers can seamlessly transition between C and Z shapes, maximizing efficiency and productivity in their operations.4. Stable iron cast structure:The CZ interchange purlin roll forming machine is built with a robust iron cast structure, ensuring stability during the forming process. This sturdy framework enhances the machine's durability, minimizes vibration, and guarantees consistent and precise performance. Manufacturers can rely on this stable platform to deliver high-quality products consistently.Applications of CZ Interchange Purlin Roll Forming Machines:1. Construction industry:CZ interchange purlin roll forming machines play a pivotal role in the construction sector. These machines can effortlessly shape and process materials for roofing systems, walls, and structural supports. By offering interchangeable C and Z shapes, they provide the versatility necessary to meet the varied needs of modern construction projects.2. Infrastructure development:The CZ interchange purlin roll forming machine's ability to handle different thicknesses of material makes it a valuable asset in infrastructure development. From highway guardrails to bridges and tunnels, these machines can produce structurally sound components that withstand the rigors of heavy-duty applications.3. Industrial and commercial applications:CZ purlins find extensive use in industrial and commercial buildings. By utilizing CZ interchange purlin roll forming machines, manufacturers can produce precisely shaped purlins that seamlessly integrate into a wide range of structures. These purlins serve as a vital structural element, providing stability and support.Conclusion:CZ interchange purlin roll forming machines offer a revolution in steel processing, enabling manufacturers to efficiently shape materials for diverse applications. With the ability to handle different material thicknesses and switch between C and Z shapes effortlessly, these machines are a testament to the advancements in the industry. By investing in a CZ interchange purlin roll forming machine, manufacturers can streamline their production processes, enhance product quality, and expand their range of offerings.
High-Quality Roof Panel Roll Forming Machine for Steel Metal Roof Panels - Roofing Sheet Roll Former, 5 Ton Capacity
PLC Steel Metal Roof Panel Roll Forming Machine: The Game Changer For Roofing Sheet ProductionIn the construction industry, metal roofing sheets provide the perfect alternative to traditional roofing materials. It is no secret that traditional roofing materials are prone to various types of damage that require repair and maintenance, costing both time and money. On the other hand, metal roofing sheets offer superior durability, resistance to weather elements, and long-lasting performance, making them the preferred option for homeowners and contractors alike. However, the production of metal roofing sheets can be a complex process. This is where the PLC Steel Metal Roof Panel Roll Forming Machine comes in handy. This cutting-edge technology offers the perfect solution for businesses involved in the production of metal roofing sheets.What is a PLC Steel Metal Roof Panel Roll Forming Machine?A PLC Steel Metal Roof Panel Roll Forming Machine is an automated production line that transforms metal sheets into roofing panels. It applies the principle of roll forming to shape the sheets into the desired roofing panel design. With this machine, it is possible to create a wide variety of roofing panel designs, from corrugated panels to standing seam panels.This machine features a Programmable Logic Controller (PLC) that ensures precise, accurate, and repeatable production processes. The PLC controls the machine's operations, including the feeder, roll forming process, and cutting system. It also features an Human Machine Interface (HMI) that enables operators to monitor and control the machine during production.How does a PLC Steel Metal Roof Panel Roll Forming Machine work?The PLC Steel Metal Roof Panel Roll Forming Machine is a multi-step process that involves various stages, including:1. Metal sheet loading - This involves inserting the metal sheets into the machine's feeder.2. Sheet leveling - This stage ensures that the metal sheets are uniform and flat before they enter the roll forming process.3. Roll forming - This is the heart of the process. The metal sheets pass through a series of rollers that shape them into the desired roofing panel design.4. Cutting - Once the metal sheets have been formed into the roofing panel, the machine's cutting system cuts the panel to the desired length.5. Stacking - Finally, the roofing panels are stacked and ready for delivery.Advantages of using a PLC Steel Metal Roof Panel Roll Forming Machine1. Improved efficiency - The PLC Steel Metal Roof Panel Roll Forming Machine is designed to handle large volumes of metal sheets, enabling businesses to produce more roofing panels in a shorter time.2. Precise and accurate - The PLC controls the machine's operations, ensuring consistent and repeatable results.3. Reduced labor costs - The automated process eliminates the need for manual labor, reducing labor costs and increasing productivity.4. Customizable - The machine can be tailored to produce a wide variety of roofing panel designs, depending on the client's requirements.5. Reduced waste - The roll forming process ensures minimal waste, optimizing material usage and reducing costs.6. Enhanced safety - The machine's automated system ensures that the production process is safe for operators.In conclusion, the PLC Steel Metal Roof Panel Roll Forming Machine is a game-changer for metal roofing sheet production. It offers improved efficiency, accuracy, and customizability, reducing costs and increasing productivity. With this technology in hand, businesses can produce high-quality metal roofing sheets that meet their clients' needs and exceed their expectations.